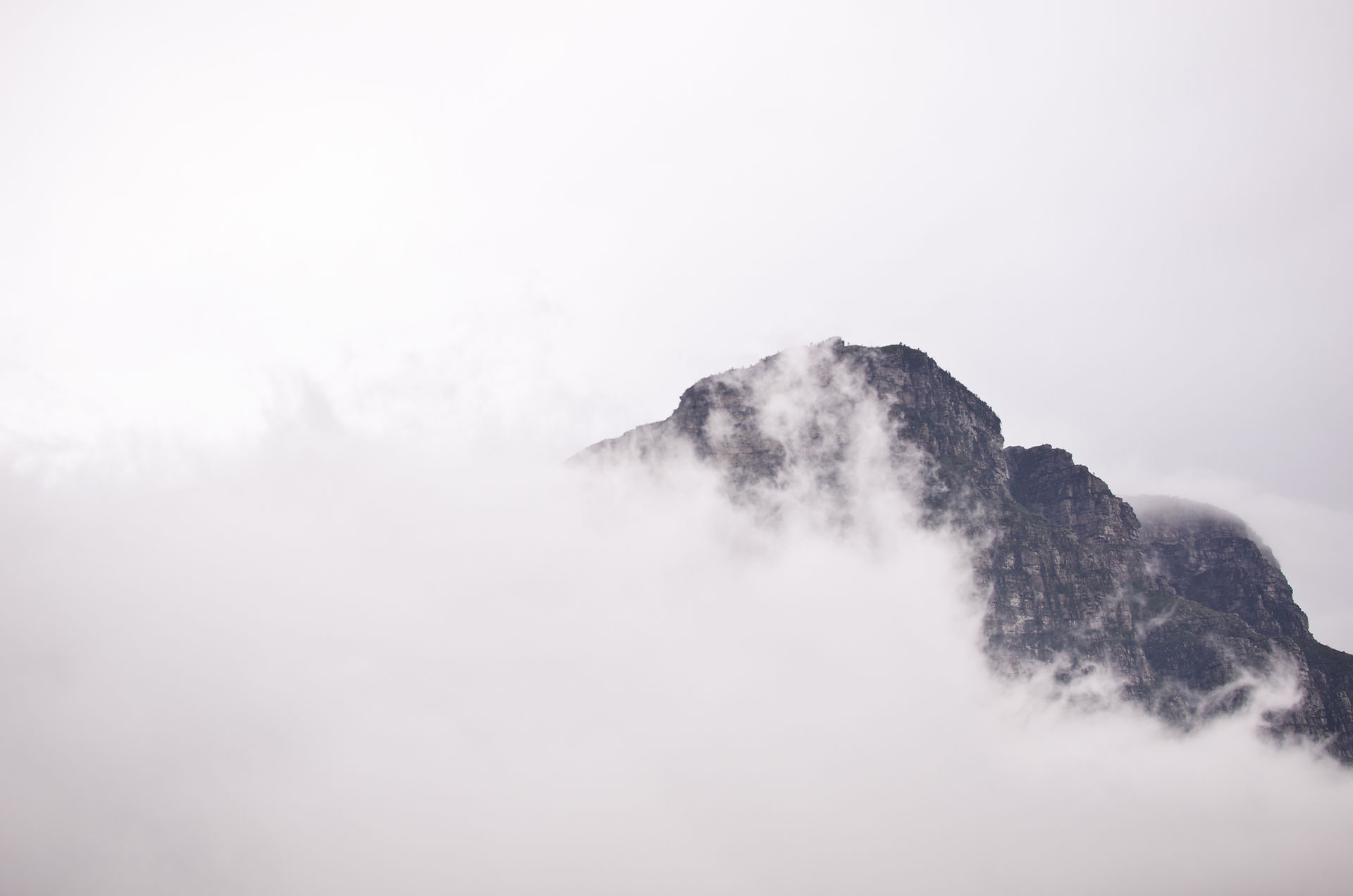
The images below highlight a few of the milestones that had a huge impact on the Company bottom line.

Optimization for Extreme Conditions
Optimized equipment to minimize exposure to H2S in an offshore well in Kazakhstan. The reservoir fluid contained 25% H2S.
Completed the extremely hazardous, dangerous, high-profile production test under extreme arctic conditions. The entire operation was executed without a single HSE incident

Development Optimization
Incorporation of the observations derived from well-test analysis from 5 wells in Nigeria resulted in a new geologic and reservoir model that matched historical production data.
This resulted in an optimized field-development plan
Logistics
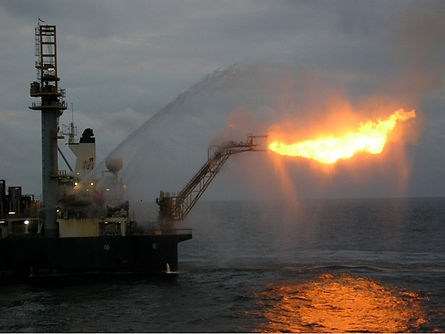
In a span of 5 weeks, designed and supervised a high-temperature production test. Equipment and personnel required mobilization to Equatorial Guinea from 17 countries.
Excellent teamwork and collaboration among different units resulted in a successful operation without a single HSE incident. All test objectives were met.
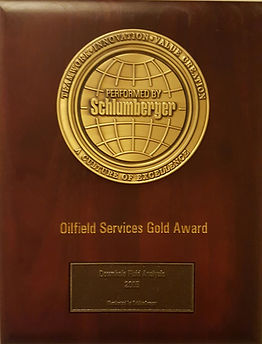
New Technology
Collaborated with Schlumberger-Doll scientists to develop and test a statistical downhole-fluid analysis algorithm in a Nigeria deepwater exploration well to detect similarity of nearby fluids dowhole. The Nigeria team adopted this technique in all future deepwater wells, which decreased field-development plans by 2 years.
Received Gold Medal and Plaque from Schlumberger

Setting World Record with Tractor
In Sakhalin, established world record of 9750 meters with downhole PLT string that ran in hole via a hydraulic tractor. Creative engineering allowed sending pressure and temperature gauges downhole in an ingeniously designed empty TCP-gun carrier with a special connector to the PLT string.
Addition of rollers to the BHA assembly allowed the PLT+gauge string to roller-skate down the borehole in a few hours, saving approximately 17 hours of tractoring time

Coal-Bed Methane
On location for the first-ever - in ExxonMobil history - Injection-Falloff Tests in a Coal-Bed Methane (Coal-Seam Gas) play in Germany. Collaboration with the reservoir engineer in the interpretation of the downhole data on-site allowed for modifications to the program to ensure that objectives were met.
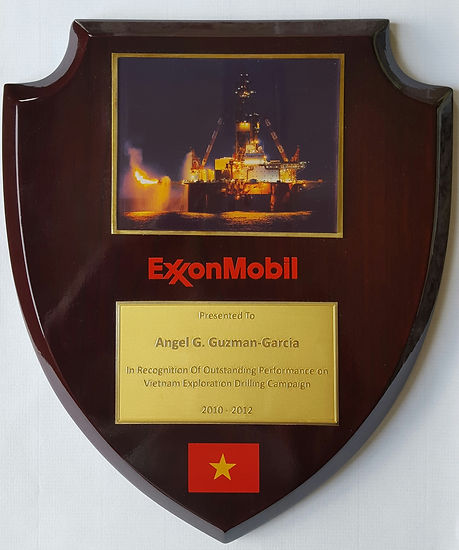
CO2 and H2S in Flow Stream
After a mock-up of all surface and downhole equipment followed by a thorough QA/QC process because of concerns with fluid composition, some modifications to the equipment were deemed crucial to ensure safe operations. Successfully completed the hazardous, high-profile production test in Vietnam. The test was executed without a single environmental, personnel, or safety incidents
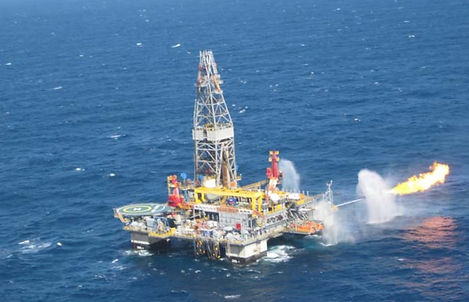
Flexibility
At a last-minute request, replaced well-test engineer to supervise a deep-water gas test in Northwestern Australia, from a DP vessel. This high-risk test required constant supervision of equipment & personnel to ensure safe operations. Downhole conditions were ideal for hydrate formation, methanol was injected both at surface and downhole. Despite multiple completion problems, all test objectives were met.

Shale Gas
Attending meetings in Budapest to progress the first shale-gas project. Careful planning of operations was required to meet objectives of the initial 3-well commitment.
This is a group photograph of the teams from ExxonMobil and TXM after the deal had been formalized.

Risk Assessment
During a visit to Aktau, a mock-up of the Surface Test Equipment was laid out and the entire ExxonMobil engineering team was present to understand concerns with traditional ways to carry out a well test.
Modifications to minimize exposure to H2S while operating under arctic conditions in an ecologically pristine area were risk-assessed by the team.

Geological Model for Deepwater Turbidite Systems
Successfully worked with a team of geoscientists to develop the geologic model for three deep-water fields in Nigeria. The work involved the integration of geology, geophysics petrophysics, and full-core analysis.